Now, linear motion technology has become a foundational element in achieving high-speed, high-precision automation. From semiconductor manufacturing and robotics to medical equipment and advanced printing systems, linear motion solutions drive innovation by enabling smooth, controlled movement along a straight path.
Unlike traditional rotary mechanisms, linear motion systems eliminate the need for complex mechanical linkages, resulting in faster response times, reduced maintenance, and unparalleled accuracy. This article delves into the fundamentals of linear motion technology, what it is, how it works, and why it’s essential for next-generation industrial performance.
What is Linear Motion Technology?
Linear motion technology refers to the engineering systems and components that enable controlled movement in a straight line, rather than rotational motion. This technology forms the backbone of many modern automation solutions, particularly in industries that demand precision, speed, and repeatability.
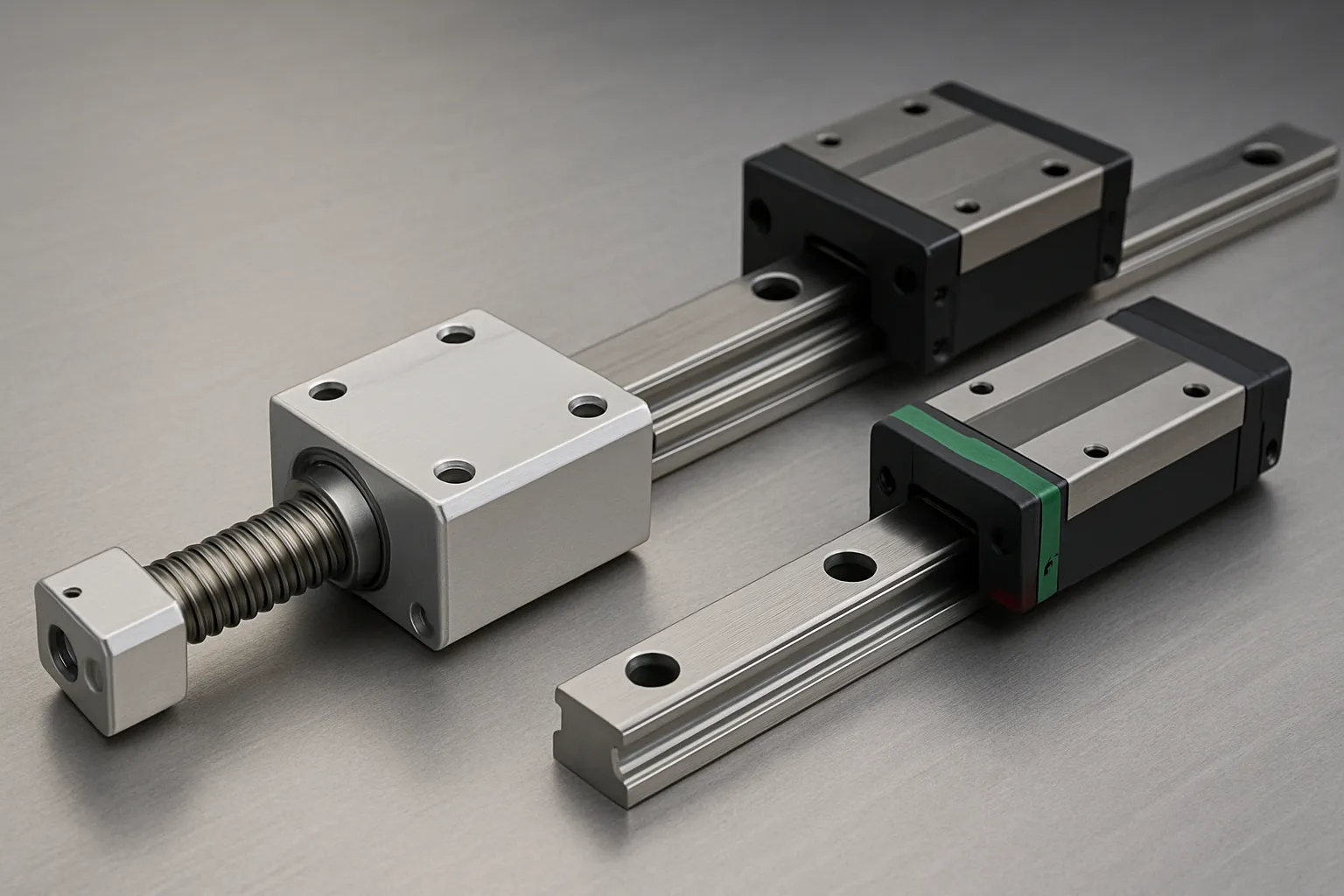
At its core, linear motion involves converting electrical energy into mechanical energy that moves an object or tool along a straight path. This movement can be achieved using various mechanisms, but in advanced industrial applications, linear motors have become the preferred choice due to their efficiency, compact design, and low maintenance requirements.
Linear motion systems typically consist of several key components working in harmony:
- Linear motors, which generate direct linear force without the need for intermediate mechanical parts such as screws or belts.
- Linear guides and bearings, which ensure smooth and stable motion by reducing friction and maintaining alignment.
- Encoders or sensors, which provide real-time feedback to control position, velocity, and acceleration with high accuracy.
One of the defining features of linear motion technology is its ability to eliminate mechanical backlash and minimize energy loss. Unlike traditional rotary motors that require complex transmission systems to produce linear motion, direct-drive linear systems simplify the mechanical structure and significantly improve responsiveness and durability.
By enabling high-speed positioning with nanometer-level accuracy, linear motion technology has become essential in sectors like semiconductor fabrication, CNC machining, metrology, and medical device manufacturing. Its ability to deliver precise control in compact, clean, and maintenance-friendly packages makes it an ideal solution for next-generation automation challenges.
In summary, linear motion technology is not just about moving objects in a straight line, it’s about doing so with efficiency, intelligence, and precision that traditional systems can no longer match.
Core Components of Linear Motion Systems
A well-designed linear motion system relies on the seamless integration of multiple core components, each playing a vital role in ensuring smooth, accurate, and reliable motion along a straight path. Understanding these components is essential for selecting the right solution for any given application.
1. Linear Motors
At the heart of most advanced linear motion systems lies the linear motor. Unlike conventional rotary motors, linear motors produce direct thrust along a straight axis without converting rotary motion. There are two primary types of linear motors:
- Iron-core linear motors offer high force density and are ideal for heavy-load applications. However, they may exhibit cogging effects due to the interaction between the coils and the iron core.
- Ironless linear motors are designed for ultra-smooth motion with zero cogging, making them ideal for precision-critical applications such as metrology, semiconductor inspection, and biomedical devices.
- Vacuum-compatible linear motors are specifically built to operate in cleanroom or vacuum environments where contamination must be minimized.
The choice of motor type depends on performance requirements such as force output, speed, thermal management, and smoothness of motion.
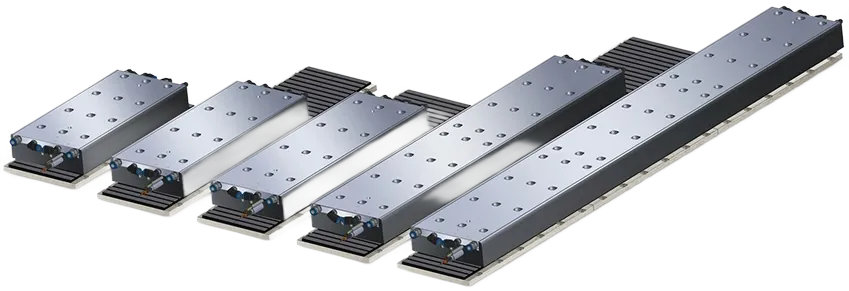
2. Linear Guides and Bearings
While the motor provides the thrust, linear guides and bearings ensure stability and control. These components support the moving element and guide it along a straight trajectory, minimizing friction and misalignment.
Linear guides typically consist of a rail and a carriage, designed to absorb loads and maintain rigidity across long strokes. Precision-grade bearings, such as cross-roller or recirculating ball bearings, help achieve smooth motion even under high dynamic loads.
The quality of the guiding system significantly impacts system longevity, accuracy, and repeatability, especially in high-speed applications.
3. Position Feedback Devices (Encoders)
To achieve precise motion control, modern linear systems incorporate position feedback devices, most commonly encoders. Encoders detect the position of the moving element and transmit real-time data to the motion controller, enabling closed-loop control of position, velocity, and acceleration.
There are two main types of encoders:
- Incremental encoders, which provide relative position changes.
- Absolute encoders, which provide the exact position, even after power loss.
High-resolution encoders are essential in applications that demand sub-micron or nanometer-level accuracy. The integration of feedback ensures smoother motion profiles, minimizes overshoot, and enhances safety during operation.
4. Controllers and Drives
To function effectively, linear motion technology components require motor drives and motion controllers. The drive powers the motor, while the controller interprets commands, calculates trajectories, and communicates with feedback systems to coordinate real-time adjustments.
Advanced controllers can manage multiple axes, support complex motion profiles, and integrate with higher-level automation systems or industrial networks.
By understanding these key components and how they interact, engineers and system integrators can design custom linear motion solutions that meet specific performance goals while ensuring long-term reliability and scalability.
Advantages of Linear Motion Technology
Linear motion technology brings transformative benefits to precision-driven industries. By enabling direct, controlled movement along a straight path, it offers performance advantages that are difficult to match with conventional mechanical systems. Here are five core benefits that make linear motion systems a smart choice for modern automation:
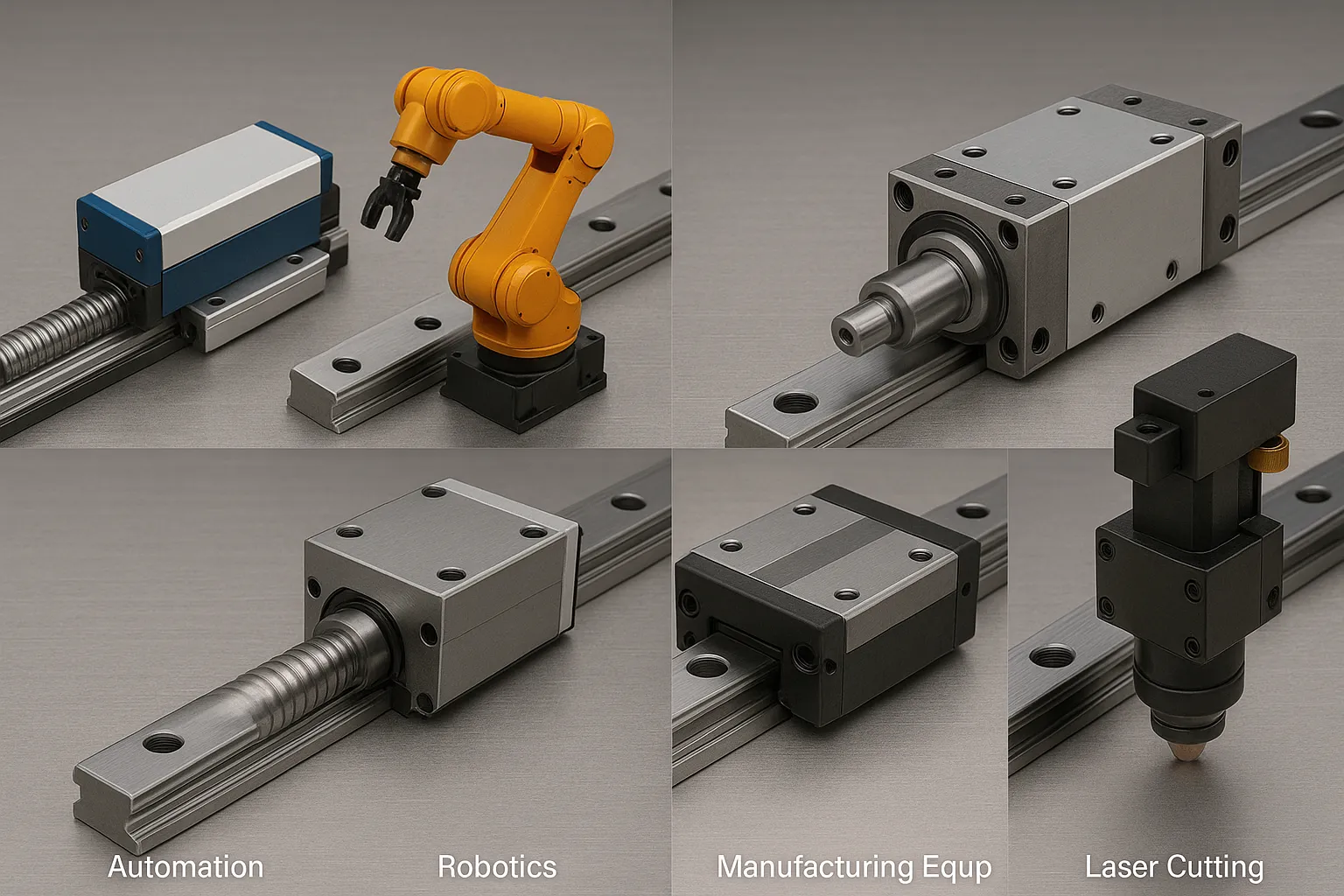
1. High Precision and Repeatability
Linear motion systems excel in delivering exceptionally accurate and repeatable positioning. This is largely due to the direct-drive mechanism and integration of high-resolution encoders, which eliminate backlash and reduce system variability. Industries such as semiconductor manufacturing, laser machining, and biomedical automation rely on this level of precision to maintain process integrity and quality control.
2. Faster Speeds and Acceleration
Without the limitations of belts, gears, or screw drives, linear motors provide direct thrust to the moving load. This results in faster response times, higher peak velocities, and greater acceleration capabilities. In production environments, this translates into shorter cycle times and increased throughput without sacrificing motion quality.
3. Low Maintenance and Long-Term Reliability
Because linear motion systems have fewer mechanical parts in contact, they experience less wear over time. Ironless linear motors, for example, operate without friction between moving components, eliminating the need for lubrication and reducing maintenance downtime. This leads to a lower total cost of ownership and greater operational uptime.
4. Smooth and Stable Motion
Cogging, vibration, and mechanical noise are common challenges in traditional motion systems. Linear motion technology particularly when using ironless motors delivers extremely smooth, vibration-free travel. This is crucial for applications that require stable movement, such as precision inspection, scanning, or optical alignment.
5. Compact Design and Cleanroom Compatibility
Linear motion components are often compact and modular, making them easy to integrate into systems with limited space. Many are also available in cleanroom or vacuum-compatible configurations, which are essential in fields like electronics manufacturing and life sciences where contamination control is paramount.
Applications of Linear Motion Technology
The versatility of linear motion technology has made it a foundational element in many high-performance industrial and scientific applications. From automated manufacturing lines to precision laboratory instruments, linear systems enable controlled, repeatable movement that is vital for quality and efficiency. Below are some of the most common and impactful use cases:
1. Semiconductor and Electronics Manufacturing
In semiconductor fabrication, linear motion systems power equipment for wafer inspection, photolithography, and die bonding. These processes demand micron or even sub-micron positioning accuracy and vibration-free operation, making linear motors an ideal solution.
2. Medical and Laboratory Equipment
High-precision linear motion plays a critical role in diagnostic machines, DNA sequencers, robotic surgical systems, and liquid handling equipment. In these sensitive applications, smooth motion and cleanroom compatibility are essential to ensure both accuracy and hygiene.
3. Industrial Automation and Robotics
Linear motion systems are widely used in pick-and-place machines, CNC tools, and robotic arms. Their ability to move loads quickly and precisely enhances production speed, repeatability, and flexibility across various manufacturing sectors.
4. Packaging and Material Handling
In high-speed packaging lines, linear actuators control cutting, sealing, sorting, and labeling processes. Their fast acceleration and consistent accuracy help maintain product quality and reduce waste.
5. Optical and Imaging Systems
Linear motion is essential in camera positioning, scanning stages, and laser beam alignment. Smooth, jitter-free movement is critical in applications like 3D scanning, microscopy, and lithography, where any vibration can distort results.
6. Aerospace and Defense
In flight simulators, satellite positioning mechanisms, and precision test rigs, linear motion systems provide stable, programmable movement that meets the stringent performance and safety requirements of aerospace applications.
How to Choose the Right Linear Motion System
Choosing the ideal linear motion system depends on matching technical performance with your specific operational needs. Here are the key factors to consider:
- Load Capacity: Understand how much weight the system must carry and how much force is required. Both static and dynamic loads matter, especially if the system must accelerate or decelerate rapidly.
- Precision & Repeatability: Does your application demand high accuracy? For tasks like semiconductor inspection or surgical automation, consider systems offering micron or sub-micron precision.
- Speed & Acceleration: High-speed production lines or scanning applications need systems that can move quickly without sacrificing control. Linear motors often outperform traditional lead screws here.
- Environment Conditions: Will the system operate in cleanrooms, humid environments, or dusty factory floors? Choosing systems rated for your environment sealed units, corrosion-resistant materials, or vacuum-ready components may be necessary.
- Motor Type Selection
- Ironless motors: Offer smooth, cog-free motion; great for lightweight and precision work.
- Iron-core motors: Provide higher force output; suited for heavy-duty applications.
- Integration & Space Constraints: Check the available space in your machinery and ensure compatibility with your control systems. Modular and compact designs simplify installation and future expansion.
- Total Cost of Ownership: Evaluate not just the purchase price, but also long-term costs such as energy usage, maintenance needs, and potential downtime.
Selecting the right linear motion system is not a one-size-fits-all decision. It requires a careful evaluation of performance requirements, environmental conditions, and long-term operational goals. By understanding your specific needs from load handling to precision and integration you’ll be in a better position to choose a system that delivers consistent performance, minimizes downtime, and supports your business objectives.
Conclusion
Linear motion technology is more than just a mechanism, it’s the backbone of modern automation and precision engineering. From factory floors to surgical robots, it enables smoother, faster, and more accurate movement across countless industries. By understanding what it is, how it works, and where it can be applied, you’re better equipped to choose the right solution for your specific needs.
Whether you’re building a high-speed production line, designing lab automation, or upgrading legacy systems, investing in the right linear motion system is key to unlocking performance, efficiency, and innovation.