According to Interact Analysis (2023), the global collaborative robot (cobot) market is experiencing a compound annual growth rate (CAGR) of 20%, projected to reach $2.3 billion by 2027. As industries increasingly rely on automation, the demand for precision, repeatability, and efficiency is placing traditional motion systems under pressure. Technologies like ball screws and timing belts, once sufficient, are now creating bottlenecks in modern cobot design.
To meet the rising expectations of Industry 4.0, ITG has developed high-performance linear motors that eliminate mechanical limitations and unlock a new level of capability in collaborative robotics. Backed by recent data from McKinsey, nearly 60% of smart factories will adopt direct-drive systems by 2027, it is a trend ITG is helping accelerate.
The Limits of Traditional Motion Systems in Cobots
While traditional motion control components like ball screws and belt-driven actuators have been industry mainstays, their mechanical nature introduces several drawbacks when applied to modern cobot applications.
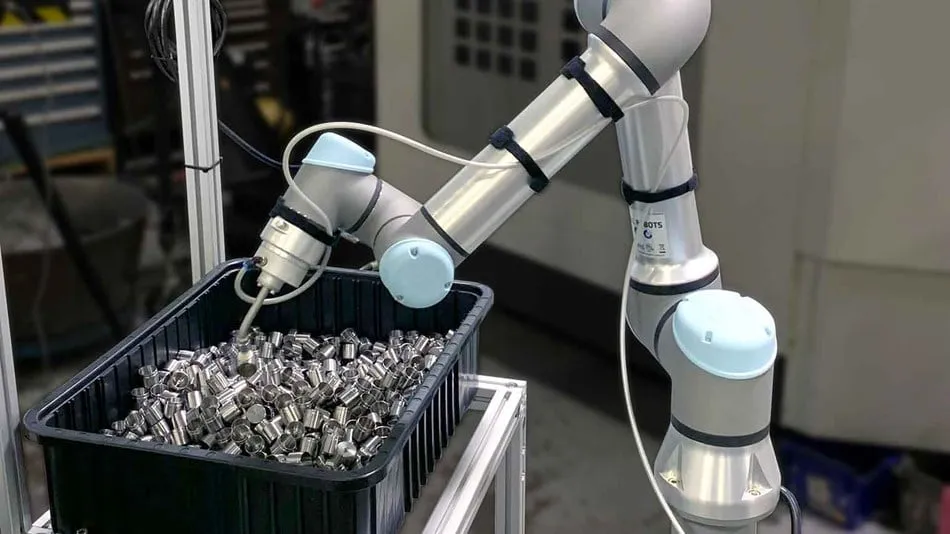
- Backlash and Inaccuracy: Mechanical systems often suffer from backlash, the lost motion due to gaps between components. For high-precision cobot tasks, this becomes unacceptable. Ball screws may offer repeatability of around 5 µm, while ITG linear motors achieve sub-micron accuracy, often <1 µm, ensuring optimal performance for advanced tasks.
- High Maintenance Requirements: Components such as belts, gears, and bearings wear over time and require ongoing maintenance or replacement. According to Fraunhofer IPA (2022), downtime due to component failure is a growing concern in automated production lines, leading to increased operational costs.
- Bulky Designs Limit Flexibility: The physical size of traditional systems also poses challenges. In an era where cobots are expected to work side-by-side with humans, compact design is crucial. Mechanical systems often restrict the ability to create small-footprint, high-performance machines, whereas linear motors support slim, modular, and flexible designs.
The World Robotics Report 2023 by the International Federation of Robotics (IFR) further confirms that companies adopting advanced drive systems are seeing better uptime, faster deployment, and higher output quality.
Why ITG Linear Motors Are the Ideal Solution
To overcome the limitations of mechanical systems, ITG has developed a comprehensive portfolio of linear motor solutions tailored for cobots offering unmatched precision, speed, and reliability.
To better understand the core principles behind this technology, read our in-depth article: What is a linear motor.
Two major product families stand out in cobot integration: the IL (Ironless) Series and the IC (Ironcore) Series.
Ironless Motors (IL Series): Optimized for Precision Cobots
Ironless linear motors offer completely cog-free operation, which results in ultra-smooth motion ideal for sensitive tasks such as micro-assembly or printed circuit board (PCB) handling. With acceleration rates of up to 10 m/s² and sub-micron repeatability, these motors significantly enhance productivity in high-speed pick-and-place applications.
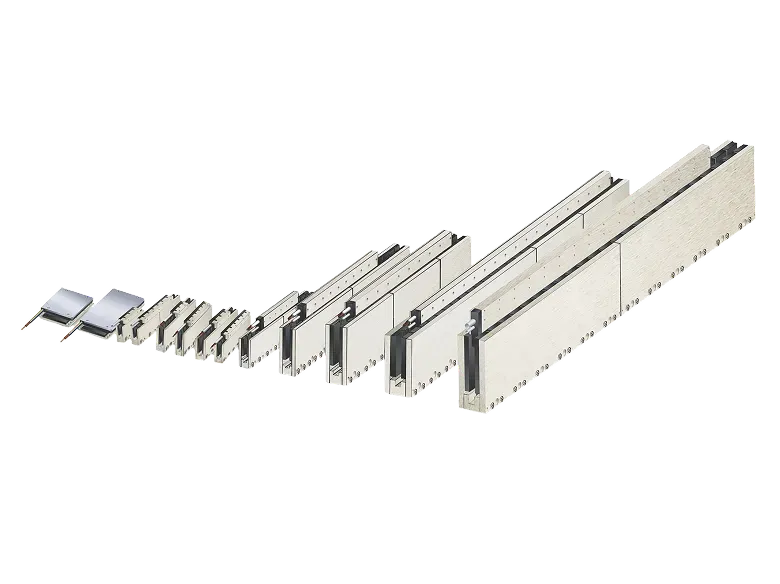
In a recent deployment, a pharmaceutical automation firm used ITG’s IL series for lab automation. The cobot achieved consistent 0.5 µm repeatability, outperforming traditional belt-driven systems and allowing for faster throughput with higher accuracy.
Ironcore Motors (IC Series): Designed for High-Force Applications
For more demanding industrial environments, ITG’s IC series provides continuous thrust forces of up to 1,500 N nearly double that of competing models. These motors feature a compact design with patented thermal management, enabling uninterrupted 24/7 operations without performance degradation.
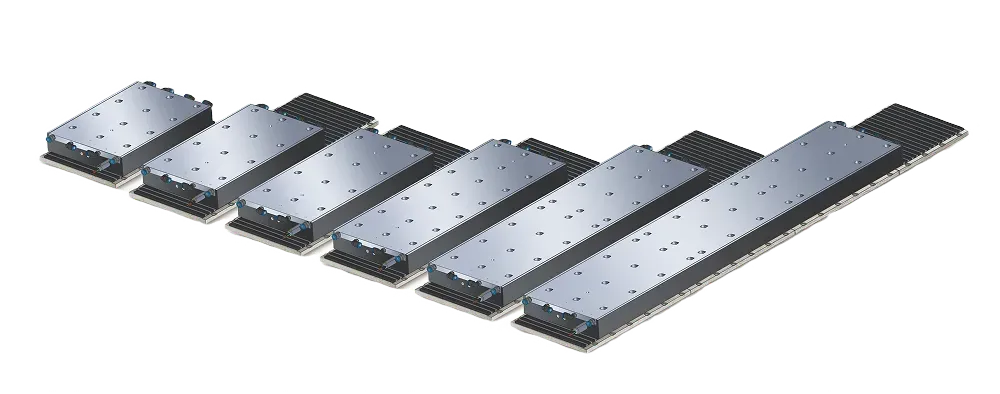
The IC series is especially effective in high-load assembly tasks, welding automation, and metal-handling cobots where force and durability are critical.
Real-World Impact: Case Study about Linear Motor
One of ITG’s most compelling success stories involves a major automotive manufacturer seeking to increase productivity on its final assembly line. The company had relied on ball screw-driven cobots, but the systems began showing wear, causing delays and increased maintenance costs.
After switching to ITG’s IC series linear motors, the client recorded:
- A 30% reduction in cycle time
- A 45% decrease in downtime due to mechanical failure
- Improved placement accuracy of automotive parts
- Reduced long-term maintenance expenses by over 40%
This powerful combination of real-world results and cutting-edge engineering proves why ITG’s linear motors are more than just components, they are the driving force behind the next generation of collaborative robots.
Whether you’re building precision-driven lab automation or high-force industrial cobots, ITG offers a tailored solution that delivers unmatched performance, reliability, and scalability. In a world where every micron and every millisecond matters, ITG linear motors don’t just meet expectations, they redefine them.
The Future: ITG Linear Motors and Industry 4.0
As manufacturing rapidly evolves toward smarter, more autonomous operations, the demands on automation technologies are rising in both complexity and sophistication. In the era of Industry 4.0, cobots are no longer expected to simply execute repetitive tasks, they are being transformed into intelligent systems capable of real-time data acquisition, self-optimization, and seamless integration with interconnected factory ecosystems.
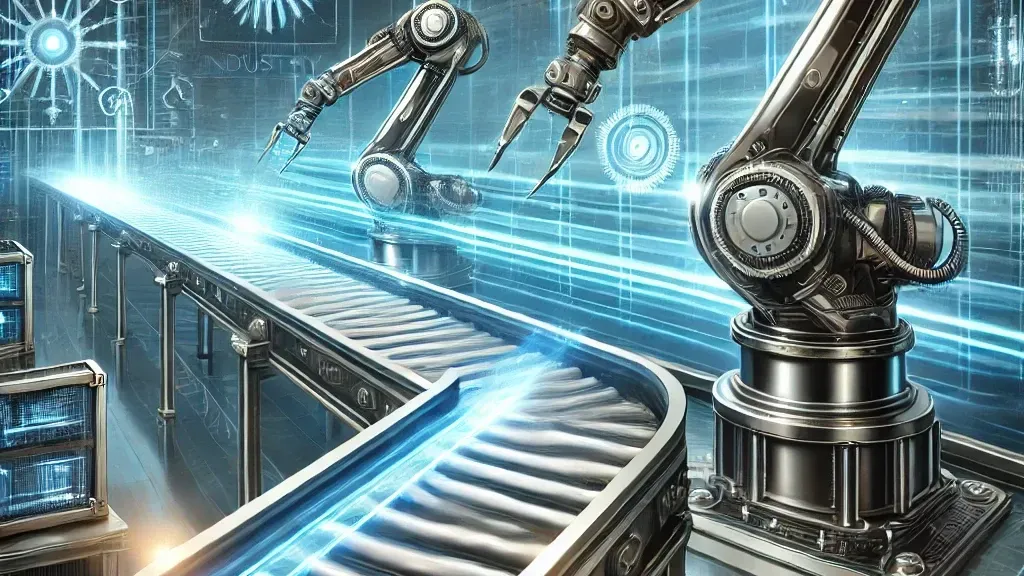
At the heart of this transformation lies the need for motion solutions that are not only fast and precise, but also intelligent, adaptable, and energy-efficient. ITG’s next-generation linear motors are engineered precisely for this purpose. Designed with Industry 4.0 at their core, these motors support direct integration with IoT platforms, edge computing systems, and cloud-based analytics, making them an essential building block for the factories of the future.
Smart Sensing and Predictive Maintenance
One of the standout features of ITG’s linear motor systems is their built-in intelligence. By embedding sensors that monitor critical parameters such as temperature, vibration, and load, these motors enable predictive maintenance strategies that can detect anomalies long before they result in costly downtime.
This data can be transmitted in real time to centralized monitoring dashboards or machine learning platforms, allowing manufacturers to forecast potential failures, schedule maintenance more effectively, and extend the lifespan of both machines and production lines. The result is a more stable and cost-efficient production environment, exactly what Industry 4.0 demands.
Energy Efficiency and Environmental Impact
Sustainability is no longer a secondary concern, it’s a strategic priority. With growing pressure to reduce carbon footprints and meet ESG (Environmental, Social, and Governance) goals, manufacturers are turning to more energy-conscious solutions. ITG’s linear motors consume up to 30% less energy than traditional pneumatic or hydraulic actuators, making them a green alternative that doesn’t sacrifice performance.
This efficiency translates into substantial long-term savings on operational costs while supporting broader environmental targets. For companies looking to meet strict sustainability benchmarks without compromising production speed or precision, ITG offers the ideal solution.
A Market Poised for Transformation
According to Statista (2024), the global smart factory market is on track to reach $1.5 trillion by 2030, driven by the adoption of intelligent systems, real-time analytics, and automation technologies.
With its innovative linear motor technology, ITG is strategically positioned to be a leader in this transformation, powering a new generation of cobots and machines that are smarter, faster, and greener.
As the line between physical machinery and digital intelligence continues to blur, ITG’s high-performance linear motors will remain a critical enabler of intelligent manufacturing, paving the way for a future where efficiency, insight, and automation go hand in hand.
Conclusion
With the cobot market growing rapidly and the shift toward smart factories accelerating, traditional motion systems are no longer sufficient. ITG’s linear motors are the foundation for next-generation automation, delivering unmatched precision, reliability, and efficiency for collaborative robots in any industry.
Ready to upgrade your cobot’s performance? Contact our engineering team today for a tailored solution that meets your production goals.