Linear motion refers to the movement of an object or component along a straight path, a concept that lies at the core of countless automation systems today. From CNC machines and robotic arms to advanced medical devices and semiconductor production lines, linear motion systems enable fast, precise, and repeatable operations.
This article covers what linear motion is, how it works, key system types, and its vital role in today’s industries. If you want to boost performance and stay ahead in automation, understanding linear motion is a smart move.
What is Linear Motion?
Linear motion is the backbone of modern automation. It refers to motion along a straight path, as opposed to rotary motion which occurs around an axis. Whether it’s in high-speed packaging, precision robotics, or semiconductor manufacturing, linear motion systems are the invisible engine driving performance, speed, and accuracy.
In the context of industrial automation, linear motion is not just a mechanical concept—it’s a strategic advantage. With the right linear motion control systems and drives, businesses can execute ultra-precise positioning, seamless material transport, and synchronized multi-axis coordination at scale.
There are several types of linear motion systems, including:
- Direct-drive systems using linear motors (e.g., ironless or ironcore),
- Ball screw or lead screw systems for mechanical actuation,
- Belt-driven systems for longer travel ranges with moderate accuracy.
Each technology delivers unique benefits, depending on the application demands for force, accuracy, and cost efficiency.

Why Linear Motion Is Critical in Automation and Engineering
The linear motion industry has exploded alongside the demand for smarter, faster, and more precise automation. From medical imaging equipment to industrial robots, linear motion technology plays a vital role in enabling compact designs, reducing maintenance, and pushing throughput to the limits.
Here’s why you should care:
- Unmatched precision: Execute movements with micrometer accuracy.
- Zero backlash: Eliminate mechanical gaps for ultra-smooth operations.
- High repeatability: Achieve consistent performance every single time.
- Scalable design: Adapt from small lab systems to massive production lines.
In an era where downtime costs dollars and every millisecond counts, choosing the right linear motion drives can directly influence your bottom line.
Linear Motion vs. Rotary Motion: What’s the Difference?
While rotary motion involves spinning around an axis (like a motor shaft), linear motion is all about moving straight whether that’s up/down, in/out, or side to side. Rotary motion is great for rotation-driven tools or wheels, but when precision placement or straight-line travel is required, linear motion is the clear winner.
When Should You Choose Linear Over Rotary?
Choose linear motion technology when your application demands:
- Precision movement over a defined axis
- High dynamic responsiveness without mechanical conversion losses
- Smooth, vibration-free operation (e.g., in optics or cleanrooms)
Real-World Examples:
- In semiconductor fabs, ironless linear motors power wafer handlers with zero cogging.
- In pick-and-place machines, belt-driven linear actuators ensure fast, reliable part movement.
- In medical scanners, high-precision linear stages control scanning arms for accurate diagnostics.
Operating Principle and System Architecture
How Linear Motion Works
What is linear motion, really? It’s the controlled movement of an object in a straight line with no curves, no compromises. In the context of modern engineering, linear motion represents precision, power, and performance without rotational conversion. This is not just physics; it’s the foundation of high-efficiency automation.
The mechanism behind linear motion is straightforward but powerful: a drive system either mechanical (screw, belt) or electromagnetic (linear motor) generates force that propels a moving element along a linear guide. The motion is governed by a control system that dictates position, speed, and acceleration based on real-time feedback.
But here’s where the magic happens: force, friction, and accuracy don’t just influence performance they define it.
- Force determines how much load can be moved and how quickly.
- Friction impacts smoothness, energy efficiency, and component wear.
- Accuracy ensures the position is reached to the micrometer every time.
In high-stakes environments like semiconductor assembly or surgical robotics, even a minor deviation can be catastrophic. That’s why linear motion technology is engineered for zero backlash, near-frictionless travel, and unparalleled repeatability.
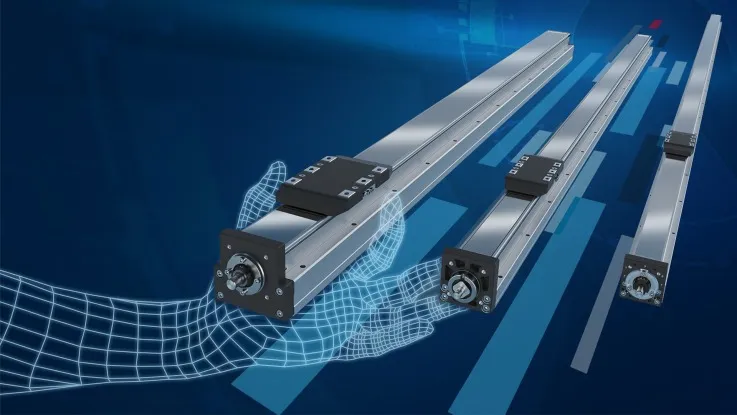
The Core Architecture of Linear Motion Systems
Every high-performance linear motion system is built on a robust architectural foundation. Whether you’re designing a compact lab instrument or a large-scale manufacturing robot, the same critical components apply:
1. Linear Guides – The Backbone of Motion
Linear guides provide the structural path for movement. Their job? Deliver smooth, stable, and accurate guidance, even under heavy loads or high speeds. High-quality guides minimize vibration and deflection key to long-term reliability in demanding applications.
Benefit: Keep your operations aligned and friction-free, no matter the distance or force involved.
2. Actuators – The Power Unit
Actuators are the muscle of the system. This is where motion is generated—either mechanically (ball screw, lead screw, belt) or directly (ironless/ironcore linear motion drives). They convert energy into straight-line movement with precision and power.
The choice of actuator determines:
- Load capacity
- Acceleration/deceleration profiles
- Resolution and travel range
Choose right, and you unlock maximum productivity.
3. Encoder, Controller & Driver – The Brain of the System
This is where smart meets strong. The linear motion control system consists of:
- Encoders to track real-time position and velocity
- Controllers to process commands and trajectory paths
- Drivers to deliver accurate electrical signals to the actuator
Together, these elements form a closed-loop system that ensures error-free, dynamic motion control, critical in industries where precision equals profit.
Most Common Linear Motion Technologies
Linear Motors
These motors generate force directly along a linear path, using electromagnetic fields instead of mechanical contact.
-
Ironless Linear Motor
The ironless linear motor is built for applications where ultra-smooth, cog-free motion is a must. With no iron in the moving coil, this motor type eliminates magnetic attraction between the coil and stator, offering virtually zero cogging force and ultra-low inertia.
Key Benefits:
- Ultra-precise movement, even at low speeds
- No magnetic pull = longer bearing life and reduced vibration
- Ideal for cleanrooms, semiconductor, laser cutting, and optical systems
When only perfection in motion is acceptable, ironless is the weapon of choice.
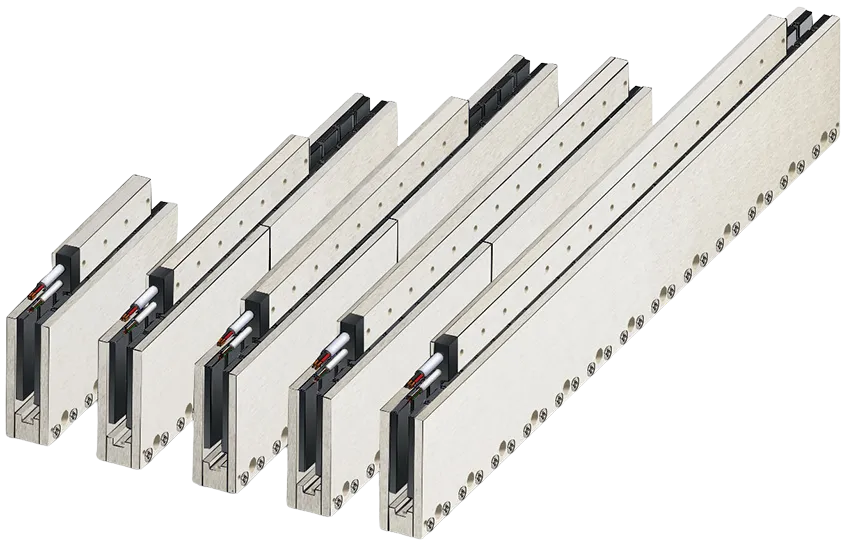
-
Ironcore Linear Motor
Need more thrust? Enter the ironcore linear motor. Built with an iron lamination core, this variant delivers higher continuous and peak forces ideal for moving heavy loads at high speeds. While it does produce some cogging, today’s motion controllers can effectively compensate for it.
Best suited for:
- Large-format automation systems
- High-speed industrial packaging
- Automotive manufacturing
If you want muscle with precision, the ironcore motor brings both to the table.

Advantages & Common Applications of Linear Motors
- Direct-drive motion: No mechanical linkages = fewer points of failure
- Minimal maintenance: No belts, screws, or lubrication required
- High-speed, high-accuracy: Critical for industries like semiconductors, medtech, and electronics
- Compact design: Shrinks machine footprint while enhancing throughput
Indirect Linear Motion Drives
For many industries, these systems translate rotary motion (from a motor) into linear movement using mechanical elements.
-
Ball Screw & Lead Screw Systems
These are the workhorses of traditional linear motion. Ball screws use recirculating ball bearings to minimize friction, while lead screws offer simplicity and cost-efficiency.
Ball Screw Benefits:
- High positioning accuracy
- Efficient power transmission
- Suitable for CNC machines, 3D printers, and machine tools
Lead Screw Advantages:
- Lower cost
- Self-locking (no back-drive)
- Great for vertical applications or low-duty cycles
If your project calls for precision without complexity, ball and lead screws remain reliable, proven choices.
-
Belt-Driven Actuators
These systems use a toothed belt and pulley mechanism to deliver fast, repeatable motion over spans of several meters.
Ideal for:
- Conveyor systems
- Light pick-and-place operations
- Packaging and material handling
Strengths:
- High speed and low noise
- Cost-effective over long strokes
- Easy maintenance and modular design
-
Rack and Pinion Systems
For applications requiring high torque and rugged reliability, rack and pinion drives provide the force. This mechanism involves a gear (pinion) engaging with a linear gear track (rack), converting rotary motion into powerful linear displacement.
Where it shines:
- Heavy-duty automation
- Large-scale industrial machines
- Environments with harsh operating conditions
Industrial Applications of Linear Motion Technology
What is linear motion’s real-world impact? Let’s explore the industries where it’s not just useful, it’s indispensable.
1. Semiconductors and Precision Electronics
This is where ironless linear motion drives dominate, offering cog-free, ultra-smooth motion critical for cleanroom environments.
- Unmatched repeatability and stability
- Zero contamination risk (non-contact drive systems)
- Compact system architecture for space-constrained tools
Whether you’re building the next-gen AI chip or assembling micro-optics, linear motion control systems deliver the motion precision your competitors wish they had.
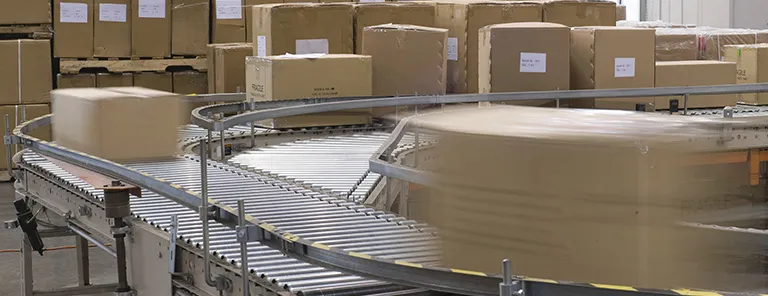
2. Industrial Automation and Robotics
Linear motion systems are the muscle behind robotic arms, automated production lines, and assembly cells in smart factories. From pick-and-place to high-speed sorting and part feeding, types of linear motion systems like belt drives, linear motors, and ball screws allow manufacturers to scale with precision.
- Faster throughput = higher ROI
- Reduced mechanical wear = lower maintenance costs
- Scalable motion architecture = future-ready factories
The linear motion industry is driving the shift from reactive manufacturing to predictive, data-driven automation.
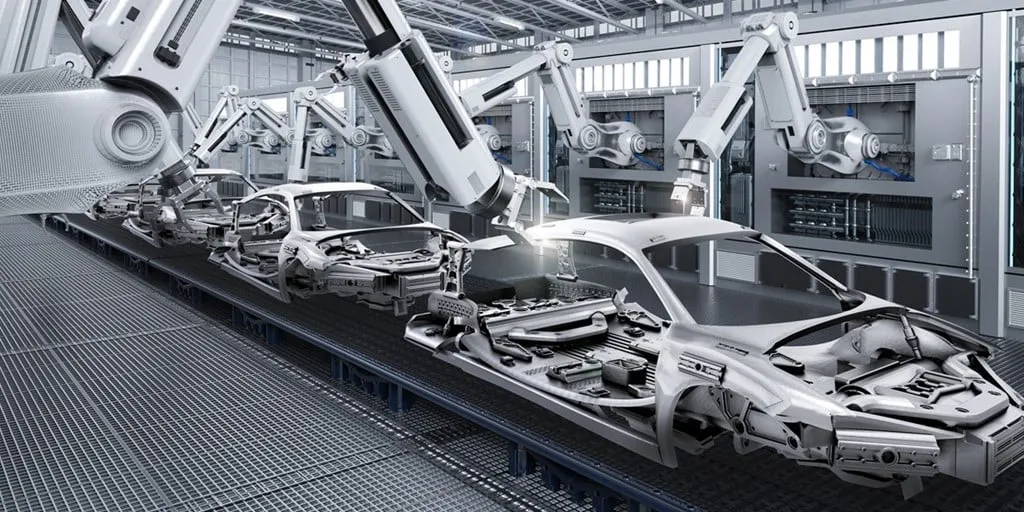
3. Medical Devices and Imaging Systems
Healthcare innovation relies on motion precision. In MRI machines, surgical robots, and diagnostic scanners, linear motion technology enables non-invasive procedures, accurate imaging, and micrometer-level instrument control.
Applications include:
- Patient tables with smooth, low-noise linear motion
- High-resolution image capture systems
- Robotic-assisted surgeries requiring sub-millimeter accuracy
4. Printing, Packaging, and Materials Automation
You need linear motion systems that keep up without breaking down. Whether it’s cutting, gluing, labeling, or stacking motion needs to be fast, synchronized, and exact.
- Seamless integration into high-throughput lines
- Reliable, long-distance motion with belt-driven actuators
- Compact, modular designs that optimize floor space
From folding cartons to industrial 3D printers, linear motion technology helps companies automate faster, waste less, and ship smarter.
Advantages and Disadvantages of Linear Motion Systems
Like any advanced solution, linear motion technology comes with both strengths and trade-offs. Let’s break it down so you can make the smartest move.
Advantages
- High speed and precision: Linear motion drives offer fast, accurate, and repeatable positioning. With direct-drive movement and no mechanical conversion, they deliver micron-level precision for critical applications in electronics, medical devices, and automation.
- No backlash and low maintenance: With fewer moving parts and no mechanical contact, these systems eliminate backlash and reduce wear. This results in smoother motion, less maintenance, and significantly longer operational life.
Disadvantages
- High initial cost: Cutting-edge performance comes with a premium price. While linear motion technology is a smart long-term investment, the upfront cost is higher than traditional mechanical alternatives.
- Requires precise installation: Proper alignment and calibration are critical. Any misalignment can impact system accuracy and durability, making professional setup a must.
- Limited travel in some configurations: Certain linear motion systems, such as ironless motors, may have restrictions on maximum stroke length. For long-range movement, alternative system types may be more suitable.
Conclusion
Linear motion isn’t just about moving in a straight line, it’s about moving smarter, faster, and with greater precision than ever before. From high-speed production lines to ultra-accurate medical devices, its impact spans across industries, enabling innovation and operational excellence. As you explore different classifications and applications, the key is to match the right linear motion system to your performance goals. In an increasingly competitive and automated world, investing in the right motion technology isn’t just an upgrade, it’s a strategic advantage.