The term servo motor linear is becoming increasingly common in motion control discussions. These motors combine the accuracy of servo technology with the efficiency of linear movement, making them well-suited for applications where precision and repeatability matter.
Whether you’re working with a servo motor linear actuator, a linear rotary servo motor, or a linear actuator with servo motor, understanding how these systems work is essential for selecting the right solution for your automation needs. This article will guide you through the basics, key types, and practical use cases of linear servo motors.
What Is a Servo Motor Linear?
A servo motor linear, often referred to as a linear servo motor, is a type of electric motor that produces linear motion rather than rotational motion. Unlike conventional rotary servo motors that require additional mechanical components like ball screws or belts to convert rotary motion into linear movement, linear servo motors generate direct linear force and displacement through electromagnetic interaction. This allows for faster response times, higher accuracy, and smoother operation in many motion control applications.
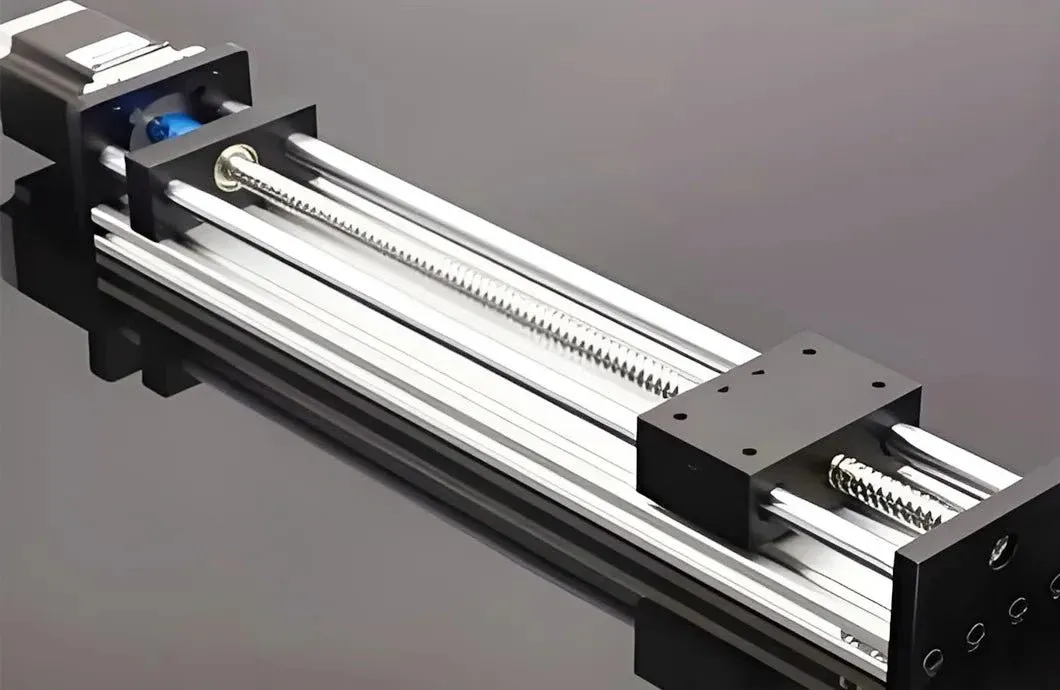
At its core, a linear servo motor typically consists of two main components: the stator (often called the forcer) and the mover (commonly referred to as the platen or magnet track). When electric current flows through the coils of the stator, it interacts with the magnetic field of the mover, producing a controlled linear force. The movement is precisely regulated through a feedback mechanism such as an encoder or linear scale, enabling the motor to follow specific motion profiles with high accuracy.
One of the defining characteristics of a servo motor linear system is its closed-loop control. This means that the motor continuously receives feedback about its position, speed, and force, allowing real-time adjustments to maintain accuracy even under varying loads or conditions. This capability makes it highly suitable for tasks that demand high dynamic performance, such as pick-and-place operations, semiconductor handling, and high-speed machining.
In addition to performance, linear servo motors offer several design advantages. Their non-contact structure minimizes mechanical wear, which leads to longer operational life and reduced maintenance. They also provide greater design flexibility, as the motor can be customized to fit compact or complex systems without the spatial constraints imposed by rotary-to-linear mechanical conversions.
In summary, a servo motor linear is a direct-drive motion device engineered for precise, efficient, and reliable linear motor movement. It plays a critical role in modern automation systems where traditional rotary motors fall short in speed, accuracy, or complexity.
Common Types of Servo Motor Linear Systems
Servo motor linear systems are available in various configurations, each designed to meet specific motion requirements across different industries. Understanding the distinctions between these types helps engineers and system integrators select the most suitable solution for their application.
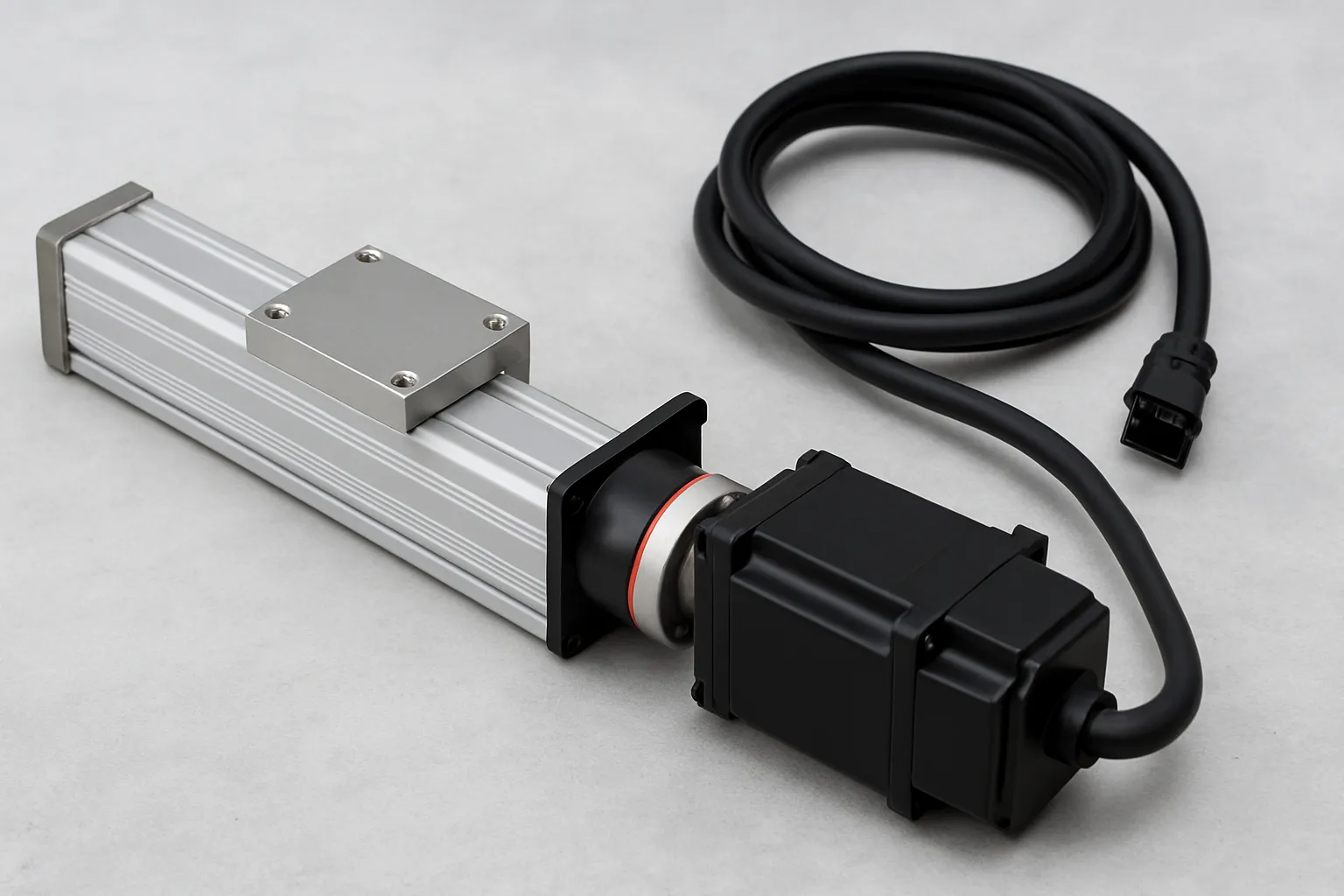
Below are the most common types:
1. Servo Motor Linear Actuator
A servo motor linear actuator is a system that combines a servo motor with a mechanical actuator to deliver linear movement. Unlike traditional actuators that rely on rotary motors and screw mechanisms, a linear servo actuator often integrates the motor directly into the motion path, eliminating conversion stages and increasing overall efficiency.
These actuators are ideal for applications requiring precise positioning, such as automated inspection systems, CNC tools, and 3D printers. Their key advantages include high acceleration, smooth travel, and accurate control of speed and position. Depending on the setup, they may include additional components such as guide rails or feedback encoders to ensure stability and repeatability.
2. Linear Rotary Servo Motor
A linear rotary servo motor combines two motion axes in one compact unit providing both linear and rotary motion from a single device. This hybrid system is commonly used in robotic arms, assembly systems, and tasks involving both pick-and-place and torque control in a single cycle.
By integrating rotary and linear movement, these motors reduce space, simplify wiring and control systems, and enhance synchronization. Their built-in feedback systems ensure seamless transitions between motions, making them especially useful in multi-axis operations where time and footprint are critical.
3. Linear Actuator with Servo Motor
A linear actuator with servo motor is a more modular approach, where a rotary servo motor is coupled with a separate linear actuator such as a lead screw, ball screw, or belt-driven stage. This configuration is widely used in retrofitting existing systems or when a specific actuator form factor is required.
While it doesn’t offer the same direct-drive benefits as a true linear servo motor, this type of system can still provide excellent precision and control when properly tuned. It is often more cost-effective and easier to integrate into conventional machine designs, making it a popular choice in packaging, material handling, and automated testing.
These variations of servo motor linear systems each have unique strengths and limitations. Choosing the right one depends on your application’s required speed, load capacity, motion complexity, and available installation space. In the next section, we’ll explore real-world use cases where these motors deliver measurable performance advantages.
Applications of Servo Motor Linear Systems
Servo motor linear systems are widely used in industries where precise, repeatable linear motion is essential. Thanks to their high speed, accuracy, and dynamic response, these motors offer significant advantages over traditional motion solutions.
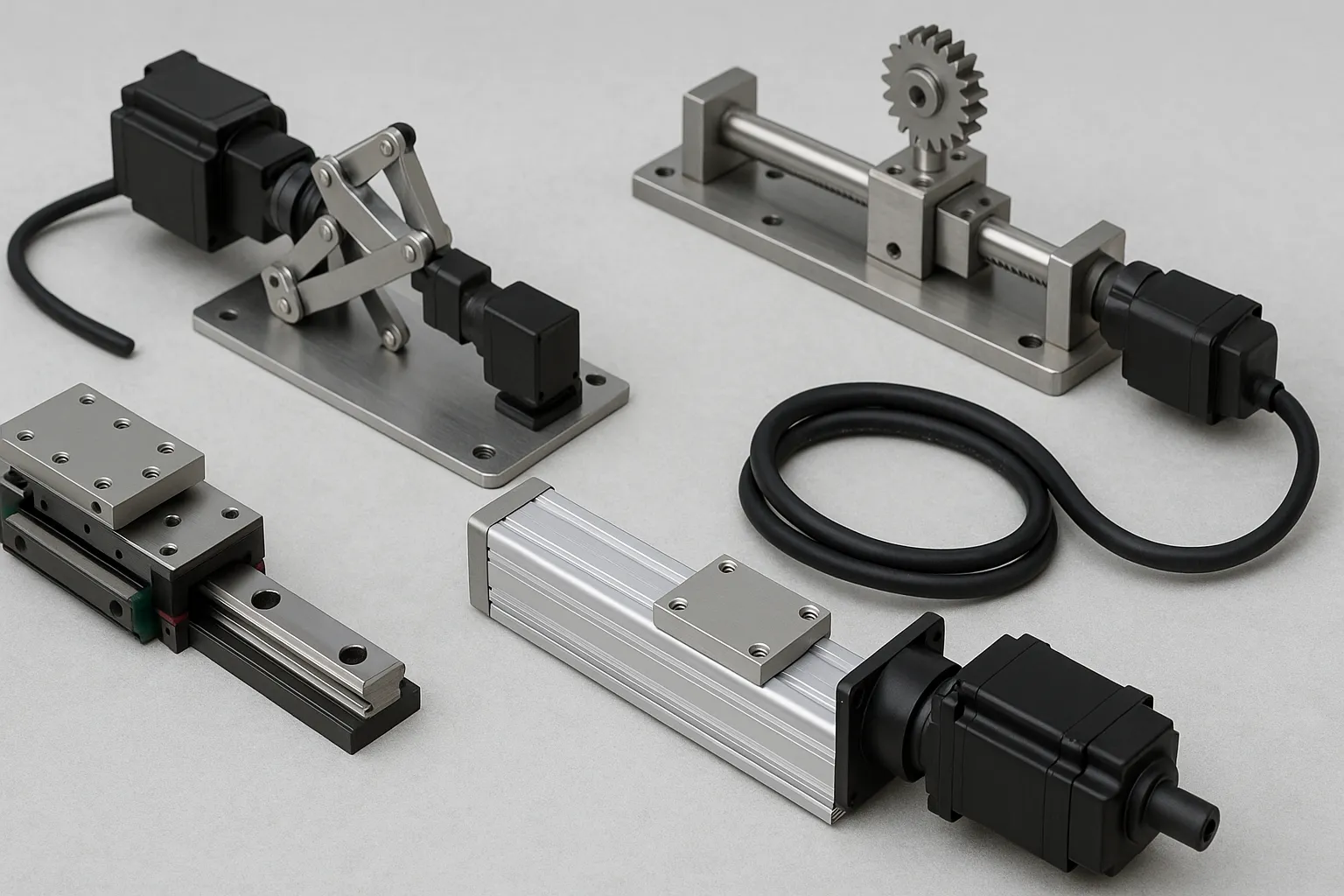
Here are some of the most common applications:
1. Industrial Automation and Robotics
In advanced manufacturing environments, servo motor linear actuators are used for tasks such as high-speed assembly, material handling, and robotic positioning. Their ability to deliver direct linear motion allows for faster cycle times and reduced mechanical complexity compared to systems using rotary motors with conversion mechanisms.
2. Semiconductor and Electronics Manufacturing
In the semiconductor industry, linear servo motors are essential for wafer inspection, lithography, and precision metrology equipment. The motors’ smooth motion and nanometer-level resolution make them ideal for sensitive, clean-room environments where vibration and particle generation must be minimized.
3. Medical and Laboratory Equipment
Medical devices and diagnostic machinery often require compact, silent, and highly accurate motion control. Linear actuators with servo motors are used in applications like MRI tables, sample transport systems, and automated laboratory workflows, ensuring consistent and safe operation.
4. CNC Machines and Precision Machining
Linear rotary servo motors are commonly integrated into CNC tools to perform simultaneous linear and rotational cutting operations. This dual-axis control enables greater flexibility in part design, improves cutting accuracy, and reduces the need for multiple tooling stations.
5. Packaging and Printing Equipment
In high-speed packaging lines, linear servo motors help control product positioning, sealing, and labeling with exact timing and alignment. Their responsiveness and repeatability enhance throughput while reducing mechanical wear, downtime, and maintenance costs.
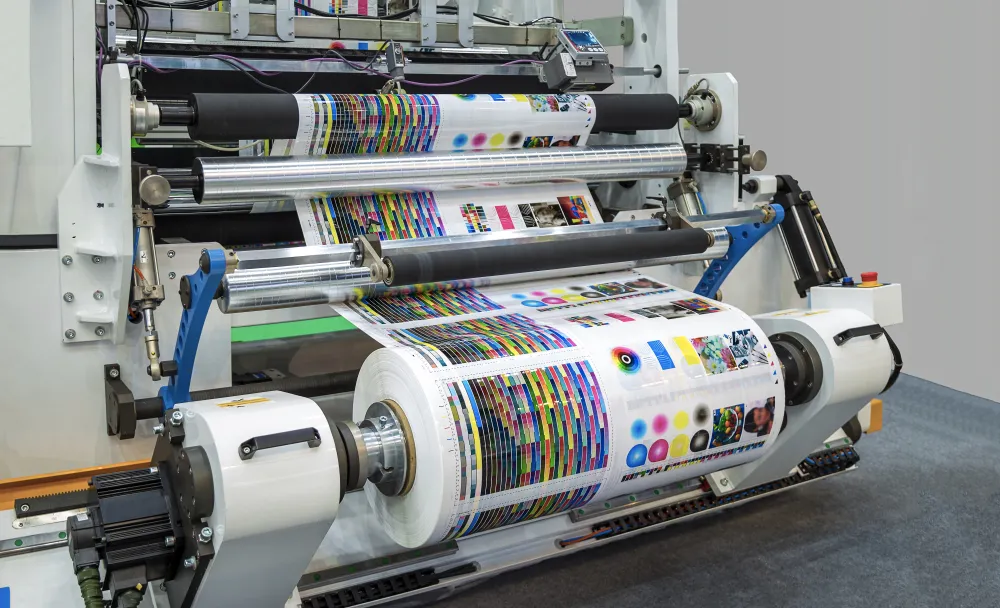
6. Aerospace and Defense
In mission-critical applications such as satellite assembly, flight simulators, and missile guidance systems, the reliability and accuracy of linear servo motors are crucial. These motors support synchronized multi-axis control, high shock resistance, and long operational life.
Servo motor linear systems continue to expand into new sectors as automation demands increase. Their adaptability and performance make them a smart investment for engineers and manufacturers aiming to improve precision, efficiency, and overall system reliability.
How to Choose the Right Servo Motor Linear for Your System?
Selecting the appropriate servo motor linear for your application is a critical step that affects performance, reliability, and integration success. Below are the key factors to consider when evaluating and specifying a linear servo system:
1. Define the Motion Requirements
Start by determining the motion profile:
- Stroke length – How far does the actuator need to move?
- Speed and acceleration – What are the target cycle times?
- Positioning accuracy – What level of precision is required (e.g., micron or sub-micron)?
Understanding these requirements helps narrow down compatible motor models and configurations.
2. Consider the Load Characteristics
Evaluate both the moving mass and the load type (vertical, horizontal, cantilevered, etc.). Make sure the motor can handle the peak and continuous forces necessary to move the load while maintaining accuracy. Over-sizing can increase cost and energy use, while under-sizing risks failure or underperformance.
3. Choose the Right Feedback and Control System
Linear servo motors typically require high-resolution encoders or linear scales for accurate position feedback. Choose a feedback system that matches your control precision needs and integrates easily with your motion controller or PLC.
4. Evaluate Environmental Conditions
Environmental factors can significantly impact motor performance:
- Temperature extremes
- Dust, moisture, or chemical exposure
- Vacuum or clean-room requirements: Select materials and sealing options accordingly. For example, some servo motor linear actuators are specifically designed for cleanroom or vacuum-compatible operations.
5. Compare Drive and Controller Compatibility
Ensure the linear servo motor is compatible with your servo drive and motion controller. Pay attention to voltage, current ratings, and communication protocols (such as EtherCAT, CANopen, or Modbus). Some suppliers offer fully integrated systems that simplify setup and tuning.
6. Consider Maintenance and Mechanical Integration
Think about how the motor will be mounted and serviced. Direct-drive linear systems usually require less maintenance due to fewer moving parts. However, ease of access, cable routing, and mechanical fit should also be evaluated during the design stage.
By thoroughly evaluating these criteria, you can choose a servo motor linear solution that not only meets your technical requirements but also ensures long-term efficiency and system reliability. Consulting with an experienced supplier or motion control expert can help tailor the right configuration for your project.
Conclusion
As industries continue to demand faster, more accurate, and more compact motion systems, the servo motor linear stands out as a key enabler of high-performance automation. From direct-drive linear actuators to hybrid linear rotary systems, these motors offer unmatched precision, reliability, and flexibility across a wide range of applications.
Whether you’re designing a robotic arm, upgrading a CNC platform, or automating cleanroom processes, understanding the different types of linear servo systems and how to choose the right one, can make a significant difference in performance and cost-efficiency.